bolt and nut size chart pdf
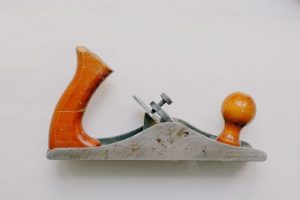
Overview of Bolt and Nut Size Charts
Bolt and nut size charts provide standardized specifications for dimensions, thread pitches, and strengths, ensuring compatibility and safety in mechanical applications. Referencing ASME B18.2.1, these charts are essential for selecting the correct hardware for projects, guaranteeing proper fitment and performance across various industries.
Bolt and nut size charts are detailed tables that provide standardized measurements for bolts and nuts, ensuring compatibility and safety in mechanical applications. These charts typically include dimensions like diameter, thread pitch, and length, as well as specifications for hexagonal and socket head types. Adhering to standards such as ASME B18.2;1 and ISO metrics, they help users select the correct fasteners for their projects. By referencing these charts, professionals can ensure proper fitment, prevent fastener failure, and maintain uniformity across industries. They are indispensable tools for engineers, mechanics, and DIY enthusiasts alike.
Importance of Using Bolt and Nut Size Charts
Using bolt and nut size charts is crucial for ensuring proper fitment, safety, and efficiency in mechanical applications. These charts provide precise measurements and standards, helping to prevent fastener failure and ensuring structural integrity. By referencing these guides, professionals can avoid costly errors, reduce assembly time, and maintain compliance with industry standards. Proper sizing also enhances performance and durability, making these charts indispensable for engineers, mechanics, and DIY projects. They are essential tools for achieving accuracy and reliability in any fastening application.
Standard Bolt and Nut Sizes (US)
US standard bolt and nut sizes are specified in ASME B18.2.1, covering hex bolts from 0 to 3 inches. Charts provide precise diameters, thread pitches, and lengths for accurate selection.
Common US Bolt Sizes and Dimensions
US standard bolt sizes range from 0 to 3 inches, with precise dimensions outlined in ASME B18.2.1. Charts detail major and minor diameters, thread pitches, and lengths for hex bolts. Common sizes include 1/4″, 1/2″, and 3/4″, with varying thread counts. Bolt heads feature standard widths and heights, ensuring compatibility with wrenches and sockets. Materials like carbon steel and stainless steel are specified, along with optional coatings. Printable PDF charts simplify selection, offering a quick reference for diameters, thread specifications, and head markings. Proper sizing ensures structural integrity, safety, and efficiency in mechanical applications.
Thread Pitch and Length Specifications
Thread pitch and length are critical in bolt and nut size charts, ensuring proper fitment and torque. Coarse threads (e.g., 12UN, 16UN) are common for general use, while fine threads (e.g., 24UN, 32UN) are used for high precision. Length specifications vary by bolt type, with standard lengths ranging from 1/4″ to 3″. Charts detail thread class fits (1A, 2A, 3A), pitch diameters, and major/minor diameters. For example, a 1/2″-13UNC bolt has a 1/2″ major diameter and 13 threads per inch. Proper thread and length selection ensures optimal performance and safety in assemblies.
Hex Bolt and Nut Dimensions
Hex bolts and nuts are standardized for compatibility and strength. Charts specify head width, thickness, and bolt diameter/length. For example, a 1/2″ hex bolt has a 7/8″ head width and 5/16″ thickness. Nut dimensions include width across flats (1-1/16″) and height (7/16″). Thread pitch and class (e.g., 13UN) ensure proper torque and fitment. Materials like steel, stainless steel, or zinc-plated options are detailed, with finishes enhancing durability. Accurate sizing is crucial for safe and reliable assemblies in construction, machinery, and automotive applications.
Metric Bolt and Nut Sizes
Metric bolt and nut sizes range from M1 to M36, providing standardized diameters, pitches, and thread specifications. ISO standards ensure consistency, with detailed charts for precise selection and compatibility.
Standard Metric Bolt Sizes (M1 to M36)
Metric bolts range from M1 to M36, with standardized diameters and pitches. Each size specifies major and minor diameters, thread pitch, and length. For example, M3 bolts have a 3mm diameter, while M10 bolts are 10mm. Charts detail coarse and fine thread pitches, ensuring compatibility. ISO standards govern these specifications, providing consistency globally. Engineers and manufacturers rely on these charts to select bolts that meet project requirements, ensuring proper fitment and strength. Printable PDFs simplify reference, offering a quick guide for metric bolt and nut selection across industries.
Metric Thread Pitch and Tolerance Ranges
Metric bolts feature standardized thread pitches, with coarse and fine options. For example, M1.6 bolts have a 0.35mm pitch, while M10 bolts have a 1.5mm pitch. Tolerances ensure precision, with diameters like 5.02mm to 5.12mm for M3 bolts. These specifications guarantee compatibility and proper fitment. ISO standards define these ranges, ensuring consistency across manufacturers. Printable charts provide clear reference, simplifying selection for engineers and fabricators. Proper thread alignment and torque depend on these precise tolerances, critical for safe and reliable assemblies in machinery and construction.
Nut Dimensions for Metric Bolts
Metric bolt nuts have standardized dimensions to ensure proper fitment. For example, M3 nuts have a diameter of 5.50mm, while M4 nuts measure 7.00mm. Heights range from 3.00mm for M3 to 5.50mm for M5. Width tolerances are tightly controlled to guarantee compatibility with bolts. ISO standards specify these dimensions, ensuring consistency across manufacturers. Printable charts provide detailed tables for quick reference, covering sizes from M1.6 to M36. Proper nut dimensions are critical for safe and reliable fastening in industrial and automotive applications, preventing assembly issues and ensuring structural integrity.
Bolt and Nut Materials and Finishes
Bolts and nuts are made from carbon steel, stainless steel, and zinc-coated materials for durability and corrosion resistance, with finishes ensuring long-lasting performance.
Common Materials for Bolts and Nuts
Bolts and nuts are typically made from carbon steel, stainless steel, or zinc-coated materials for strength and durability. Carbon steel is the most common, offering excellent strength at a lower cost. Stainless steel, such as grades 304 and 316, provides superior corrosion resistance, ideal for marine or outdoor applications. Zinc-plated materials offer rust resistance, while brass and nylon are used for specialized applications requiring electrical conductivity or insulation. These materials ensure bolts and nuts perform reliably across various industrial and construction environments.
Surface Finishes and Coatings
Surface finishes and coatings enhance the durability and resistance of bolts and nuts to environmental factors. Common finishes include zinc plating, chrome plating, and hot-dip galvanizing, which protect against corrosion. Stainless steel coatings are ideal for high-corrosion environments. Additionally, specialized coatings like nylon or epoxy are used for electrical insulation or chemical resistance. These finishes ensure bolts and nuts maintain their integrity and performance in harsh conditions, while also improving their visual appeal. Proper coatings are crucial for extending the lifespan of fasteners in industrial and outdoor applications.
Stainless Steel and Other Corrosion-Resistant Options
Stainless steel bolts and nuts are highly resistant to corrosion, making them ideal for marine, chemical, and outdoor environments. Grades like A2 and A4 stainless steel offer excellent durability. Other corrosion-resistant options include coated fasteners, such as hot-dip galvanized or zinc-plated bolts and nuts, which provide enhanced protection against rust. Additionally, specialized materials like titanium and silicon bronze are used in extreme conditions. These options ensure long-lasting performance and reliability in harsh applications, minimizing maintenance and replacement needs. They are widely specified in industries requiring superior corrosion resistance and strength.
Bolt Head and Nut Types
Bolt heads include hex, socket, and Torx designs, offering versatility for various applications. Nut types range from standard hex to specialized configurations, ensuring secure fastening solutions.
Hex Head Bolts and Nuts
Hex head bolts are the most common type, featuring a six-sided head for easy tightening with wrenches. Standard sizes range from 1/4″ to 3″ in diameter, with lengths varying to suit applications. Heavy hex nuts, designed for larger bolts, offer increased strength and resistance to loosening. Both bolts and nuts are manufactured to precise standards like ASME B18.2.1, ensuring consistent quality. Available in materials like steel, stainless steel, and coated options, they cater to diverse industrial needs, from construction to automotive applications, providing reliable and durable fastening solutions.
Socket Head and Torx-Head Bolts
Socket head bolts feature a cylindrical head with a recessed socket, allowing use with Allen wrenches for secure tightening. Torx-head bolts use a star-shaped recess, offering higher torque and resistance to cam-out. These bolts are ideal for applications requiring low profile and high torque. Charts include specifications for sizes from M3 to M6, detailing major and minor diameters, pitch, and head dimensions. They are commonly used in automotive and aerospace industries, providing a reliable and precise fastening solution with reduced risk of stripping compared to traditional hex heads.
Specialized Bolt and Nut Designs
Specialized bolts and nuts are engineered for unique applications, offering enhanced performance under specific conditions. Examples include high-strength bolts for structural applications, corrosion-resistant designs for marine environments, and vibration-resistant bolts for dynamic loads. Charts detail these specialized designs, providing dimensions, materials, and load ratings. Additionally, some designs incorporate features like nyloc nuts for locking or spring washers for added security. These components are crucial in industries like construction, aerospace, and heavy machinery, where standard fasteners may not suffice, ensuring reliability and durability in critical systems.
Bolt and Nut Strength Classes
Bolt and nut strength classes define mechanical properties like tensile strength, ensuring reliability under load. US and metric standards classify bolts (e.g., SAE Grade 5) and nuts (e.g., Class 8.8) for specific applications, with head markings indicating material grades and strength levels.
US Standard Strength Classes
US standard strength classes for bolts and nuts, such as SAE Grades 2, 5, and 8, define mechanical properties like proof load, tensile strength, and yield strength. These grades ensure bolts and nuts meet specific performance requirements. Grade 2 bolts are suitable for general use, while Grade 8 bolts offer the highest strength. Head markings, such as radial lines or numbers, indicate the grade. These standards are critical for ensuring safety and reliability in structural and mechanical applications, adhering to ASTM and SAE specifications. Proper grade selection is vital for load-carrying applications.
Metric Strength Classes (4.6, 8.8, etc.)
Metric strength classes, such as 4.6, 8.8, and 10.9, define the mechanical properties of bolts and nuts. These classes specify yield strength, tensile strength, and hardness. Class 4.6 bolts, for example, have a minimum tensile strength of 400 MPa, while class 8.8 bolts reach 800 MPa. Head markings, like “8.8” or “10.9,” indicate the class. These standards ensure compatibility and safety in international applications, adhering to ISO specifications. Proper class selection is crucial for load-bearing applications, ensuring reliability and durability in various industries.
Head Markings and Material Identification
Head markings on bolts and nuts provide critical information about their strength class, material, and manufacturer. Common markings include numbers, letters, and symbols, such as “8.8” for high-strength steel or “A” for alloy steel. These markings help identify the bolt’s tensile strength, hardness, and material type, ensuring proper selection for specific applications. Certifications like ISO or ASME standards are often included, guaranteeing compliance with international quality norms. Accurate interpretation of these markings is essential for traceability and reliability in industrial and construction projects, ensuring safety and durability in bolted joints.
Bolt and Nut Tolerances
Bolt and nut tolerances define acceptable deviations in diameter, thread pitch, and height, ensuring proper fitment and reliability. These specifications are crucial for maintaining structural integrity and performance.
Diameter and Thread Tolerances
Diameter and thread tolerances are critical for ensuring proper fitment and reliability in bolted joints. These specifications define acceptable deviations in major and minor diameters, as well as pitch. For US bolts, tolerances are standardized by ASME B18.2.1, while metric bolts follow ISO guidelines. The major diameter tolerance for a 1/2″ bolt, for example, might range from 0.509″ to 0.531″, ensuring compatibility with nuts. Similarly, thread pitch tolerances prevent misalignment. Ignoring these tolerances can lead to assembly issues or joint failure. Always reference the chart for precise values to guarantee safety and performance.
Height and Width Tolerances for Nuts
Height and width tolerances for nuts are crucial for ensuring proper fitment and functionality in bolted joints. These tolerances specify acceptable ranges for nut dimensions, ensuring compatibility with bolts. For example, a 1/2″ hex nut might have a height tolerance of 0.38″ to 0.40″ and a width tolerance of 0.88″ to 0.92″. These ranges are derived from standards like ASME B18.2.1 for US nuts and ISO for metric nuts. Adhering to these tolerances prevents issues like loose connections or jamming, ensuring safe and reliable assemblies. Always verify tolerances from the chart to avoid installation problems.
Surface Finish and Roundness Tolerances
Surface finish and roundness tolerances ensure bolts and nuts meet required quality standards. Surface finish specifications, like Ra (roughness average), are critical for preventing corrosion and ensuring proper torque. Roundness tolerances guarantee that nut faces and bolt heads are not excessively out-of-round, which could affect wrenching fit. For example, hex nuts typically have a surface roughness of Ra 6.3 to 12.5 µm and roundness tolerances of 0.01 mm. These specifications prevent mechanical issues and ensure reliable performance, as outlined in standards like ISO 898-1 for metric fasteners and ASME B18.2.1 for US sizes.
Applications and Uses
Bolts and nuts are fundamental components in industrial machinery, automotive systems, aerospace engineering, and construction. They ensure structural integrity and durability across various applications, from heavy machinery to everyday devices.
Industrial Applications of Bolts and Nuts
Bolts and nuts are crucial in industrial machinery, robotics, and manufacturing equipment. They are used to assemble heavy-duty components, ensuring stability and safety. In factories, they secure conveyor belts, pumps, and gearboxes. High-strength bolts are employed in construction machinery and cranes, while stainless steel fasteners are used in corrosive environments like chemical plants. Proper sizing and material selection, guided by bolt and nut size charts, are essential for maintaining operational efficiency and preventing equipment failure in demanding industrial settings.
Automotive and Aerospace Uses
In automotive and aerospace industries, bolts and nuts are critical for assembling engines, chassis, and aircraft components. High-strength, lightweight fasteners are essential for performance and safety. Torx-head bolts are commonly used in automotive applications for their resistance to cam-out, while aerospace-grade fasteners often feature specialized coatings for corrosion resistance. Bolt and nut size charts help engineers select the right hardware, ensuring precise fitment and compliance with industry standards like ISO and ASME, which are vital for maintaining structural integrity and durability in vehicles and aircraft.
Construction and Heavy Machinery Applications
Bolts and nuts are indispensable in construction and heavy machinery, ensuring structural integrity and durability. Heavy-duty applications like bridges, buildings, and equipment require high-strength fasteners to withstand massive loads. Stud bolts and heavy hex nuts are commonly used for their reliability in tension and shear loads; Proper sizing and material selection, as per bolt and nut size charts, are crucial for safety and performance in these demanding environments. These fasteners must meet stringent standards to handle the stresses of construction and machinery operation effectively.
How to Read a Bolt and Nut Size Chart
Understand the chart by identifying bolt diameter, thread pitch, and length. Ensure proper fitment and safety by accurately interpreting the specifications for your project needs.
Understanding Bolt and Nut Size Designations
Bolt and nut size designations include diameter, thread pitch, and length. For example, a metric bolt labeled “M8 x 1.25” indicates a diameter of 8mm and a coarse thread pitch of 1.25mm. US standards use similar designations, such as “1/2-13,” where the first number is the diameter and the second is the thread count per inch. Properly interpreting these designations ensures correct hardware selection, avoiding fitment issues. Always refer to a size chart for accurate specifications and compatibility, ensuring safety and optimal performance in any application.
Interpreting Dimensions and Tolerances
Dimensional specifications in bolt and nut size charts include diameter, thread pitch, and length. Tolerances define acceptable size variations, ensuring proper fitment. For example, a metric bolt labeled “M8 x 1.25” specifies a diameter of 8mm and a thread pitch of 1.25mm. US standards, like “1/2-13,” indicate a 1/2-inch diameter and 13 threads per inch. Charts also detail nut dimensions, such as width and height. Properly interpreting these measurements ensures compatibility and safety. Always verify dimensions against the chart to avoid sizing errors and guarantee precise assembly.
Common Symbols and Abbreviations
Bolt and nut size charts use specific symbols and abbreviations to denote dimensions and standards. For example, “M” indicates metric sizes, while “UNF” or “UNC” refers to fine or coarse thread pitches in US standards. Symbols like “ASME B18.2.1” or “ISO 4014” specify the governing standard. Abbreviations such as “THD” for thread diameter and “W” for width are common. Charts also use “L” for length and “H” for height. Understanding these symbols ensures accurate interpretation of size charts and compliance with international standards, simplifying hardware selection across industries. Always refer to the chart’s legend for clarity.
Manufacturing and Quality Standards
Manufacturing and quality standards for bolts and nuts include ASME and ISO certifications, ensuring reliability through strict quality control and traceability of materials.
ASME and ISO Standards for Bolts and Nuts
ASME and ISO standards provide strict guidelines for manufacturing bolts and nuts, ensuring dimensional accuracy, material quality, and performance reliability. ASME B18.2.1 specifies requirements for square and hex nuts, while ISO 4014 and 4032 cover metric hex bolts and nuts. These standards define tolerances, thread pitches, and mechanical properties, ensuring interchangeability and safety. Compliance with these standards is crucial for manufacturers and engineers to guarantee optimal performance in various applications, from industrial machinery to automotive systems. Proper certification ensures adherence to these global quality benchmarks.
Quality Control and Certification
Quality control and certification are critical in ensuring bolts and nuts meet industry standards. Manufacturers implement rigorous testing, including dimensional inspections and material strength evaluations. Certifications like ISO 9001 and ASME B18.2.1 provide assurance of quality and compliance. Third-party inspections further verify product integrity. Traceability through batch numbers and material certificates adds an extra layer of accountability. Proper certification ensures reliability, making it essential for applications requiring high safety standards. This process minimizes defects and guarantees consistent performance across all products.
Traceability and Material Certification
Traceability and material certification ensure bolts and nuts meet quality and safety standards. Each product is marked with batch numbers, enabling tracking from production to delivery. Material certificates, often compliant with ISO 9001, detail chemical composition and mechanical properties. These documents verify adherence to specifications like ASME B18.2.1. Certifications guarantee the use of authentic materials, ensuring reliability and performance. Traceability aids in identifying defects and implementing recalls, while certifications build trust with manufacturers and end-users. Proper documentation is essential for maintaining accountability and compliance in industrial applications.
Best Practices for Using Bolt and Nut Size Charts
Always verify the chart’s scale after printing to ensure accuracy. Use appropriate tools for measuring bolt and nut dimensions to guarantee proper fitment and safety in applications.
Selecting the Right Bolt and Nut for Your Project
Selecting the right bolt and nut involves considering material, strength class, and dimensions. Choose bolts made from carbon steel, stainless steel, or nylon for durability. Ensure strength classes like 4.6 or 8.8 match your project’s load requirements. Refer to size charts for precise diameter, thread pitch, and length measurements. Always verify tolerances to ensure proper fitment. Use the chart to identify compatible nut sizes and finishes. For critical applications, consult torque specifications to avoid over-tightening. Print the chart at actual size to measure accurately and ensure reliability in your project.
Tools Needed for Measuring and Installing Bolts and Nuts
Essential tools for measuring and installing bolts and nuts include micrometers, vernier calipers, and socket sets. A torque wrench ensures proper tightening without overloading. Screwdrivers and Allen keys are needed for socket-head bolts. Always use the correct socket size to avoid damage. Print the size chart at actual size and measure the ruler margin to confirm scaling accuracy. Proper tools ensure precise installation and prevent damage to bolts or nuts, guaranteeing safety and reliability in your project.
Printing and Scaling the Chart Correctly
Printing bolt and nut size charts at actual size is crucial for accuracy. Ensure no scaling is applied during printing. Measure the ruler in the margin to confirm proper scaling. Incorrect scaling can lead to measurement errors. Use tools like those found on boltdepot.com to verify accuracy. Proper scaling ensures precise bolt and nut selection, preventing installation issues. Always print in high resolution to maintain clarity. This step guarantees reliable data for your projects, avoiding costly mistakes. Refer to the chart’s instructions for specific printing guidelines.